Explosion Suppression Systems
Explosion suppression systems are designed to suppress or extinguish an explosion or deflagration at its onset, reducing pressure buildup that would rupture a process vessel or conveying duct. In an explosion suppression system, dynamic rate of rise or static pressure sensors are used to detect pressure buildup due to combustion and via the control panel activating suppressant bottles containing sodium bicarbonate, injecting suppressant into the airstream, cooling the temperature of the combustion fireball and reducing the explosion pressure.
The features of a suppression system over other mitigating techniques include:
- Prevents pressure build-up and secondary explosions
- Extremely fast response
- Effective where vent panels cannot be employed inside of buildings
- Can be added as an isolation component instead of a flap valve
- All IEP Technologies Suppression Systems are designed to meet or exceed standards set by the National Fire Protection Association (NFPA)
Components of an Explosion Suppression System
The basic explosion suppression system is comprised of a suppressor bottle (s), a pressure detector, and a control panel. The suppressor bottle contains the suppressant under the pressure of 900 PSI. The pressure detector views the process in real-time in order to determine if an event is occurring. It does this through a pair of sensors that sample the process based upon a predetermined Kst and Pmax. Upon activation, it sends a signal to the control panel which receives the signal from the pressure sensor and activates the release on the suppressor bottle(s).

Suppressor Bottle – eSuppressor
Suppressor Bottle – The eSuppressor™
The eSuppressor™ is a high-rate discharge extinguisher for explosion suppression and chemical isolation systems. Unique to the industry, the electro-mechanical operation allows no pyrotechnic devices required for activation. A key benefit is that all safety functions are fully monitored, which is not possible for any device employing pyrotechnic actuators, with full redundancy and third-party SIL 2 certification. The signal of events upon an explosion is the eSuppressor valve is actuated via the explosion protection control panel. The highly specified trigger mechanism allows the valve flap to open rapidly (less than 10 ms), allowing the suppressant to discharge through the nozzle system into the protected volume.
Included Features:
- Electromechanical actuator (no pyrotechnic actuators, which cannot be monitored)
- Monitored lock-out-tag-out (LOTO)
- Cylinder pressure monitoring with temperature compensation
- Third-party certification to SIL-2
- Can be installed on existing flanges to potentially replace all members of IEP’s existing family of suppressors
- Integrated LEDs to indicate suppressor status
- Valve housing: IP67 NEMA 4
- Rating: Ex II 3G/2D, Class 1 Div 2. Class II Div 1
- Transportation licenses: TPED and UN-DOT
- ATEX Approval (pending)
Options:
- Bottle sizes are available in cylinder volumes (liters) of 5, 20 , 31, and 45.
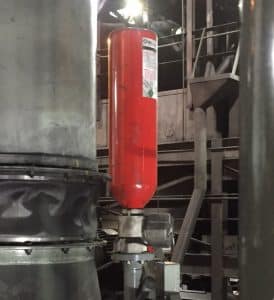
Suppressor Bottle – PistonFire II
Suppressor Bottle – PistonFire II
The PistonFire suppressor is assembled with a pressurized suppressant storage cylinder and a valve body that contains a National Electrical Manufacture Association (“NEMA”) dust-ignition-proof, weatherproof enclosure. Suppressor bottles are available in 4, 10, 20, and 30 KG sizes, preloaded, and filled with FDA-compatible sodium bicarbonate. The NEMA enclosure houses the actuating mechanism, pressure switch, pressure gauge, fill valve, OSHA supervisory switch, and field wiring connections. It is completely sealed with a screw cover and an EXP quick-disconnect connector for field wiring connections. Upon detecting an incipient explosion, the suppressor receives an actuation signal from the EX200 Control Panel. The actuating mechanism, within milliseconds, initiates the rapid release of the pressurized, dry-chemical suppressant into the protected area.
Competitive advantages include:
- DOT, TC approved – pressurized and leak-tested at the factory and shipped to the site. Pressurizing and leak testing at the customer’s facility is not required.
- Monitored and interlocked low-pressure switch per the latest version of NFPA 69
- Non-explosive initiators, safe to handle (no ATF or UN restrictions)
- Integral and standard OSHA lockout plate per the latest version of NFPA 69
- Nozzles can be inspected in place (NFPA 69). Removal or vessel entry is not required.
Spherical Bottle – HRD Dry Chemical Extinguisher
The HRD dry chemical extinguisher is like the Piston Fire in function but differs in the amount of contained suppressant (utilized on larger vessels that require more agent). It discharges suppressants in milliseconds to quench an incipient explosion within a process vessel or to block the propagation of flame through interconnected ductwork. It is a spherical refillable container constructed of a high-strength steel alloy. The extinguisher is comprised of a storage container, fill valve, burst disc valve assembly, safety plate, 30-inch long actuator cable, and an explosive triggered actuator.
Location, the number required, and the positioning of bottles on an explosion suppression system is determined by IEP Technologies engineering staff. Their knowledge and experience make them well qualified for designing and applying explosion suppression systems.
Pressure Detector – SmartDS Detection System
The MEX-3 Dynamic Rate of Rise explosion detector senses the rate of rise and differentiates between an actual explosion and normal process pressure fluctuations. This is a major factor in limiting instances of false actuations based upon process malfunctions or operator error.
Pressure Detector – Static Detector
Static Detectors are used in the most stable processes that only require one threshold. They are FM Approved and field adjustable and are sold in pairs as both must “go off” to trigger a system activation.
Optical Detector – UV/IR Detector
The UV-IR detector is used in combustible gas/vapor applications which typically involve aerosol filling or specialty chemical storage rooms. The equipment will protect the room in total and in turn, personnel. Coupled with special water-filled cylinders this is the most appropriate equipment for this application and IEP has considerable experience in this area.
Optical Detector – IR Flame Detector
The optical detectors offered from IEP include infrared and ultraviolet infrared. They can be integrated into explosion protection designs for very specific applications. The IR detector is typically used in dust collection applications where a low Kst threshold is required or vapor is present to look for a flash.
Control Panels
The EX200 or EX8000 control units are microprocessor-based and contain notification and control functions. The units utilize a power supply and battery backup feature which can be adjustable based upon the application. The Front panel window provides viewing the function happening internally to the panel for ease of viewing. When opening the unit a user can see all applicable functions that are occurring or have occurred on the backside of the control board for easy troubleshooting.
The signals coming from the sensors in the process are recorded, tested, and confirmed in the control unit and sent out to their corresponding locations according to their severity and wiring design. Important features are monitoring and activation lines being checked for wire breaks, ground faults, and short circuits continuously. Upon each start of the system, the unit goes through a self-test to confirm that it is verified electronically. The outputs provided from the units are alarms, troubles, and process interlocks.
Frequent Applications for Explosion Suppression
Explosion suppression systems are crucial and required protection needed for applications such as:
- Dust collection systems – Explosion suppression and/or isolation are common options included in these types of systems where compressed air cleaning of filter cartridges creates a dust cloud.
- Spray drying systems – An explosion suppression system is needed due to the high volume of potentially explosive material.
- Fluid bed dryers/coolers – Combustible process material requires an effective explosion suppression system.
- Flash dryers – Explosion suppression protection is needed because of the danger created by combustible dust.
- Milling systems – Combination of combustible dust and ignition hazard from moving parts necessitates an explosion suppression system.
Explosion protection is a vital part of plant processes where ignitable dust clouds are a frequent occurrence. Let SysTech with the expertise of IEP Technologies address your concerns before an issue develops.