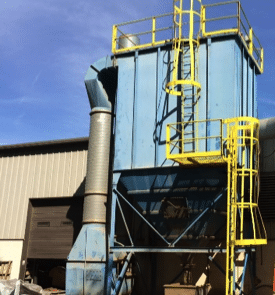
Pulse-clean baghouse, featuring 192 bags on thermal reclaim system
SysTech Design was called in to provide technical support to a foundry located near Pittsburgh Pennsylvania that was losing valuable production time due to “plugged filters” in their baghouse. The baghouse is used to reclaim a sand-type product that is cooked off during the heat treating stage of their aluminum casting process. SysTech personnel conducted an on-site analysis of the customer’s baghouse functionality, analyzing the system’s airflow, air to cloth ratio and cleaning system effectiveness.
SysTech determined that while the dust collection system’s airflow of 19,000 CFM was adequate, the current filter bags used in the baghouse were not capable of handling the particulate in the airstream. The gritty nature of the sand combined with the oil based binder was the perfect storm for creating a moisture laden, sticky dust. Shortly after system start up, the moist dust quickly caked onto the polyester filter bags, rendering the pulse cleaning system ineffective. With the baghouse down, the foundry was only able to operate one hour at a time. After one hour of production, with constant pulse cleaning taking place, the baghouse would automatically shut down as the system exceeded the maximum pre-set pressure drop setting. Subsequently, production at the foundry was forced into a standstill for almost an hour as the baghouse went through its downtime cleaning cycle without the exhaust fan running. The baghouse down time was causing the foundry to lose approximately 50% of their production output over each 24-hour period.
Dust Analysis Capability
Fully loaded standard polyester filter bag, image shown is after 4 weeks of intermittent use.
Upon completion of the on-site analysis, SysTech shipped a used polyester filter bag, as well as a dust sample to Donaldson’s chemical services lab for analyses. Donaldson, the world leader in advanced filtration, determined not only did the current polyester bags fall short of providing enough square footage of filter media to effectively manage the dust type, the bags were also not designed for the 265° F baghouse temperature. The misapplication of the polyester filter media and the high air to media ratio, was forcing the foundry to change out bags every 4 weeks.
Pleated Bag Filter Design Doubles Production Rate
SysTech proposed to retrofit the baghouse with Donaldson Torit’s pleated bag technology, using their patented SpunBond® filter media. Due to the traditional sock style footprint of the pleated bag, coupled with the cartridge filter-like design, the pleated bags offer four times the filter media found in a standard polyester bag. This allows the baghouse footprint to remain the same, while greatly increasing the filtration efficiency. The end result is increased square footage of filter media, from 3619 to 8697 square feet, which provides a much lower air to cloth ratio. Simply put, the increased media lowers the face velocity on the filters thus preventing dust impaction, this results in easier, more effective, release of particulate from the filter surface. Because of the sand binders, the pleated bags were sprayed with a hydrophobic/oleophobic coating, giving them increased resistance to the moisture and oils that are present in the dust. The SpunBond® pleated bag media was designed to withstand the 265°F airstream temperature present in the baghouse.
Significant Advantages of Pleated Bag Technology
Results of the Pleated Bag retro-fit:
Increased Production: The foundry’s heat treating process is now able to operate 24/7 allowing for a 100% increase in production, with no limits on dust collection system run time.
Decreased Pressure Drop: The operating dust collector pressure drop fluctuates between 1.5-2.5” wg. with intermittent pulse cleaning as necessary.
Increased Filter Life: Using the pleated bag technology, the lifespan of the bags has increased from 4 weeks to 6 months.
Decreased Downtime: The foundry was previously forced to work one hour on, one hour off, due to the baghouse pressure drop quickly reaching its high set point. Since the pleated bags have been installed, there are no restrictions on how long the foundry can run.
Quicker/Easier Bag Change Out: Previously, a baghouse filter change out required the manpower of two people, for two days, due to the time required to replace the existing two piece polyester sock and cage style filters. The new one piece pleated bag design allows two people to complete a 192 bag change out in just 4 hours.
Significantly Less Compressed Air Demand: Previously, the baghouse pulse cleaning system was used continually to try and overcome the misapplied polyester filter media. With the new pleated bags, the cleaning system is only in use intermittently and the compressed air requirement is 60 PSI per pulse, rather than the 90 PSI per pulse requirement for the polyester bags.
Manufacturer’s Guarantee: After analyzing the dust sample, Donaldson issued a bag life guarantee of 4000 operational hours or one year of service.
Cheaper than a new collector: The capital cost of the retrofit was 21% of the cost of a new dust collector!
As we all know, time is money. Don’t let yourself waste valuable production time due to downtime from blinded filters in a baghouse. Allow SysTech to analyze your less-than-ideal situation and start making things more productive and cost effective at your facility. We’re a phone call away 800-456-9460.