Explosion Vents
Many at-risk industrial process equipment, including dust collectors, process vessels, duct/piping networks, and industrial structures have been protected with explosion venting. Where applicable, explosion vents, also referred to as explosion panels and explosion relief panels, are a viable means to release pressure and flame propagation of a dust explosion. The strategy of explosion vents is to provide escape routes for flames and expanding gases, preventing the dangerous pressure build-up in process equipment. This will minimize damage to equipment and protect personnel working nearby.
All explosion vents we offer are as manufactured by IEP Technologies| HOERBIGER Safety Solutions and comply with NFPA 68 latest edition and ATEX. SysTech will expedite vent selection after a review of your application and based on field application experience may be able to provide alternatives and cost analysis for the final protection scheme you select.
Explosion Vent Panels for Dust Collectors & Receivers
All dust collectors (bag, envelope bag, or cartridge style), receivers, and vacuum units, after the dust is tested and analyzed, may be fitted with explosion vents as a means of explosion protection. Usually, vents are the least expensive solution. If applied, they need to be compliant with NFPA 68 “Standard on Explosion Protection by Deflagration Venting” latest edition where combustible dust is determined to be present.
Explosion Vents for Silos & Process Vessels
Silos, process vessels, and bucket elevators needing explosion protection to reduce the damage caused by a dust explosion may be fitted with explosion vents or relief panels. Explosion vents or panels have been widely used with NFPA 68 “Standard on Explosion Protection by Deflagration Venting” latest edition, the go-to manual for the design and installation for these vessels and enclosures. Vent sizing and vent area are largely determined by the Kst of the dust and the structural integrity and design of the silo or vessel.
Before we continue, we need to ask several questions:
Will an explosion vent be the practical solution? Is…
- the location of the dust collector or vessel indoor or outdoor, and what is the proximity of the vessel to an outside wall?
- there a safe path to direct gases and materials releasing through the vent?
- Is the dispelled material hazardous or toxic?
What are the initial questions we need to answer to select an explosion vent? We’ll need to know…
- dimensions of the vessel.
- Kst of the dust.
- strength of the vessel or Pred (obtained from vessel manufacturer).
- maximum explosion pressure or Pmax in Bar (from dust test results).
- Pstat -This is the activation pressure of the vent (typically set at 1.5psig).
Explosion Vent Sizing Program
At the final design stage, IEP Technologies will implement computer selection software for an explosion vent selection based on your vessel geometry. Sizing an explosion vent requires input data, some of which only you can provide and other information we will complete for you after we know more about your application. SysTech will help you with data input that you are unfamiliar with. Choose the applicable PDF data entry sheet for a Dust Collector-Round, a Dust Collector-Rectangular, or a Cyclone.
Two Major Classifications of Explosion Vents
There are two types of explosion vents available. First are Explosion Vents or Panels, which are fixed and non-resettable, and when ruptured, are positioned to direct a fireball in a calculated safe direction away from a building or structure. Second is Flameless Explosion Vents, or “indoor vents”, which are applied inside a facility and quench the explosion fireball at its source. Flameless vents are advantageous as they can be reset after an event.
Explosion Panel and Explosion Vent Construction
Explosion panels, also commonly referred to as explosion vents, are the most widely used method for mitigating or safely redirecting fireballs resulting from dust explosions.
Panels are constructed of stainless steel and include options of:
- Insulated housings
- Round or rectangular
- Flat or domed depending upon operating pressures
- Clean in-place designs
- Integrated flange gasket materials
- based on temperature
- Mounting frames
- Burst Indicators – They are positioned on the explosion vent to notify plant personnel, via electrical wiring to a control panel, of the occurrence of an event. When activated, the indicator sends a signal to a central control panel to activate a light, an alarm, or the BAS system.
Typical Explosion Vent applications:
- Dust collectors – Baghouse, Cartridge Collectors, and Cyclones
- Silos for storage and receiving
- Vacuum Systems
- Product Receivers and Conveying Systems
- Bucket Elevators
- Driers
- Duct
Advantages of IEP Technologies – HOERBIGER Safety Solutions vents:
- Standard 3 to 5-day ship time for vents – Same-day shipment for stocked vents in emergencies!
- Easy to install and maintain
- Custom designs available on quick delivery designs. This includes insulated vents on 3 to 5-day production times.
Explosion Vent Designs
Depending on the application and system pressures, IEP provides three (3) alternative vents.
1. GE or MVRD Model – Filter installations with pneumatic cleaning systems and high vacuum operations require an explosion vent that can withstand vacuum and/or positive pressure cycling for a long period of time. Its domed design enables negative pressure resistance without the need for extra vacuum support. Pressure ranges from – 2.8 PSIG to +1 PSIG on the GE vents depending on size. Pressure ranges for the MVRD Style are from – 9 PSIG to +1 PSIG. Typical burst pressures, or Pstat, are 1.45 to1.50 PSIG at standard temperatures of 68 degrees F. Standard GE and MVRD features include pressure spike tolerance and integrated flange gaskets. Nominal sizes for rectangular vents are 9” x 9” to 45” x 45”. Round vents are nominal 8” to 43” diameter. These are applied in product convey systems or vacuum type systems that require higher negative pressure designs. We also would use these on product receivers that are at the end of conveying lines.
2. KE Model – If the negative pressure is not greater than 60% of the rated opening pressure, installation of a domed vent has no extra benefit. For these applications the KE style vent is an alternative to the domed GE. The KE provides long durability and aerodynamic advantages compared to the domed type, for dust collectors such as cyclones. Pressure Ranges from – 0.7 PSIG to +0.7 PSIG. Typical burst pressures are 1.45 PSIG at standard temperatures of 68 degrees F. Pressure spike tolerance, integrated flange gaskets, cross rib and folded edges are standard KE design features. Nominal sizes from 4” x 11’’ to 40” x 80”. These may be applied in storage silos with manual feed systems or dust collectors that are commodity designs. They are ideal OEM-type vents.
3. KER Model – The KER style vent is perfect for standard applications in powder handling and storage. The KER is suitable for plant equipment with static over/under pressure conditions up to 50% of the rated rupture pressure. A unique feature with the KER is that edge reinforcement in its design allows the KER to be mounted without an outlet flange, thus reducing installation costs. Pressure ranges from -0.725 PSIG to +0.5 PSIG. Typical burst pressures are 1.45 PSIG at standard temperatures of 68 F. Cross rib and folded edges are other standard KER design features. Nominal sizes are same as KE-style vents. These are applied to dust collection systems with standard pressures of less than – 20” WC.
Flameless Explosion Vents are designed with an integral flame arrester that prevents the escape of flames in a combustible dust explosion. This allows the process vessel or dust collector to be used in a building’s interior space. Flameless vents can also be used outdoors when explosion vents can’t be safely vented, i.e., there is a road or sidewalk nearby. IEP Technologies offers two models of flameless explosion vents, the EVN, and the IV8.
IEP TECHNOLOGIES EVN FLAMELESS VENT:
During a deflation, the ATEX certified IEP EVN flameless vent valve plate compresses a spring allowing the flame and pressure wave to pass through the flame arrester. See the video for an example. There are two versions of the EVN, one that automatically reseals after an event and a second that is a non-closing version that stays held open in an explosion to be manually reset.
What does a flameless vent look like and how do they work? Take a look at the video from Hoerbiger.
Advantages of using IEP EVN flameless vents:
- A vent duct to the outside is not required – it can be used in the building’s interior
- Compact with a wide range of sizes available
- Used on smaller vessels
- Pred 2 bar (maximum)
- Kst to 300 is the maximum dust
- Up to 30% less length than standard flameless vents with more mass
- Some valves close automatically after venting – repair or refurbishment is not required
- Suitable for multiple explosions
- Options for sanitary applications
- ATEX Certified according to the latest guideline EN 16009
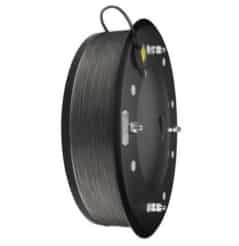
Flameless Explosion Vent – IEP Technologies – Model EVN
Like the EVN, the IV8 flameless explosion vent provides an explosion protection solution for process vessels inside a building or areas where standard explosion venting is unsafe. When an explosion occurs, the explosion vent opens, allowing the explosion pressure and flame through a flame arrestor which cools the gases and quenches the flame. Unlike the EVN, the IV8 needs a new explosion panel after deflagration. The IV8 is typically used in larger volume process vessel or dust collection applications where multiple EVNs would be required. Often, a single IV8 can replace multiple EVNs.
IV8 Included Features:
- Overall dimensions (mm) : 978 H x 990 W x 1023 L
- Pstat: 1.45 psig +/- 0.15 @ 68 ºF
- KST: ≤200 bar m/s
- MIE >3 mJ
- Weight: 150 kb
- Designed for field reconditioning
- Integrated burst sensor
- A single device can protect up to 12.3m3 and a maximum protected volume of 49.2m3
Flameless explosion vents are an alternative to traditional vent panels if the combustible dust Kst is within an acceptable range and where the vessel’s location allows its use. Like explosion vent panels, flameless vents are sized using NFPA 68 vent area calculation. To generate a vent size and quantity for a specific application, the following information is required to size a vent accurately:
- Combustible dust characteristics (KST & Pmax)
- The dirty air volume of the vessel. Unit drawing preferred
- Pressure reduced (Pred) of the vessel.
Inputting the factors above in the equation from NFPA 68, the engineers can size a flameless vent specific to your process or application.
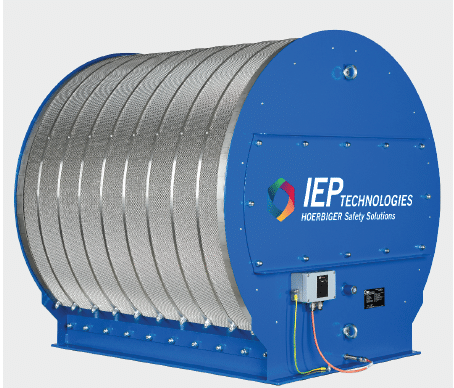
Retrofitting Explosion Vents and Panels
New construction and projects requiring vents follow a distinct pattern for selection and proper applications. Retrofitting is another issue altogether. In addition to answers required for new installations, we need to ask questions such as…
- Do we have a “safe” space around the vessel?
- Is it located indoors or outdoors?
- Is the vessel Insulated?
- Where can we discharge the vented materials should a deflagration occur?
- Is the vessel structurally sound?
- Can the Pred be verified?
- Who is the manufacturer of the vessel and is there a model number?
- What is dust Kst and Pmax – same questions as required for new installations?
- Have vent calculations been run on the vessel per current NFPA Standards?
- Has a documented Dust Hazard Analysis (DHA) been performed?
IEP Technologies/ HOERBIGER Safety Solutions has extensive application experience in designing and installing explosion venting systems. Every application should be considered unique; SysTech can assist you in determining if explosion venting is the best choice for your situation and installation questions that need to be answered upfront. All design considerations are in accordance with NFPA 68: Standard on Explosion Protection by Deflagration Venting, the latest edition.
SysTech is the place to go for your explosion panel and vent needs. We’ll show you how to get it done in a reasonable manner, at a reasonable cost, within an effective time frame that you require. Let us provide the answers and solve your problem if and when it exists – give us a call at 800-456-9460. We assist with both retrofit and new systems including matching vents by other manufacturers if a direct replacement is needed. We’re here to help!